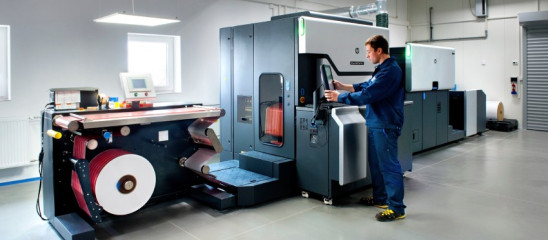
Digital, Offset, and Flexographic Printing: What Are the Differences?
When deciding how to execute a printing project, you have several options. The three main categories we utilize are digital printing, offset printing, and flexographic printing. Each has its specific characteristics, advantages, and disadvantages. Let's find out which one is best suited for your needs.When deciding how to execute a printing project, you have several options. The three main categories we utilize are digital printing, offset printing, and flexographic printing. Each has its specific characteristics, advantages, and disadvantages. Let's find out which one is best suited for your needs.
Digital Printing
Digital printing allows us to print directly from a computer without the need to prepare printing plates. We use it for small and medium runs when clients require rapid delivery. Its main advantages are:
-
An excellent choice for projects where speed and flexibility are essential.
-
A wide range of printable materials (paper, metallic, white and transparent films, combined barrier materials for flexible packaging, etc.).
-
Suitable for small series.
HP Indigo WS6600 Digital Press Takes It Even Further
It offers efficient and high-quality product presentation with perfect image and consistent colors, even for low-volume runs. HP Indigo has everything you need. Its main advantages are:
-
Frequent design changes are not a problem.
-
Zero costs for design changes.
-
Small and medium orders with a multitude of label variations.
-
Variable print data – serial numbers, EAN and QR codes, graphic elements.
-
No waiting – you get express delivery.
Offset Printing
Offset printing operates on the principle of transferring an image from a printing plate to the substrate using a rubber-covered transfer cylinder, known as the offset cylinder or blanket. The process step by step is as follows:
-
Preparation of the printing plate: The plate is usually a metal sheet with printing and non-printing areas.
-
Before applying ink, the plate is moistened with a solution of water and additives. This adheres to the non-printing areas, which repel water.
-
Ink is applied to the plate using ink rollers. The ink adheres only to the printing areas, which are oleophilic, as water on the non-printing areas repels the ink.
-
The image from the plate is transferred to the offset cylinder (blanket) covered with rubber.
-
From the offset cylinder, the image is transferred under pressure to the substrate (paper, film, etc.).
Advantages of Offset Printing
-
Excellent print quality with accurate colors.
-
Ability to use special colors (metallic shades, precise colors according to PANTONE).
-
A suitable solution for high-volume runs (thousands of pieces).
Preparing printing plates for offset takes some time, but the result is professionally looking printed materials.
We choose offset for demanding projects – it's intended for clients who require stable label quality even for million-piece runs. Offset is also used for printing catalogs, magazines, books, or representative corporate materials in large volumes, where quality and color fidelity are paramount. However, remember that it's mainly limited to paper and some films.
Heidelberg Speedmaster Simplifies the Entire Process
The Heidelberg Speedmaster meets all the demands of the current market. Thanks to extensive automation of the printing process, it is cost-effective even for smaller orders. For high-volume runs, its fast and stable production truly shines.
Flexographic Printing
Flexographic printing is a printing technology that uses flexible photopolymer printing plates. Our brand-new Soma Optima machine is ideal for printing on flexible packaging materials, paper, or laminate from roll to roll. It features the following advantages:
-
High-quality printing even on thin and flexible materials.
-
A broader spectrum of printable materials (paper, films, laminate).
-
Suitable for large volumes and long runs.
-
Efficient printing, especially for packaging and labels.
-
Ability to print with UV inks for high gloss and durability, as well as with solvent-based and water-based inks.
-
Accurate color reproduction thanks to CNC positioning and an automatic register adjustment system.
-
High production speed.
Additionally, the Soma Optima is equipped with advanced features – a central cylinder with thermal stabilization, which prevents material wrinkling or stretching, and doctor blade chambers that ensure even ink application. Efficiency and speed are further enhanced by an automatic washing system.
So, Which One to Choose? We're Happy to Advise
Still unsure which technology to choose? We'd be happy to relieve you of this dilemma. Every project is unique and has its specific requirements. Fill out the contact form, and we'll get back to you to find the best solution.